
Changing the way the world operates
in hazardous environments
​
REDEFINING MINING...
Introducing the ARTEV ™6000 - unmatched by any competitor in terms of its capability.
A world first, battery electric, rover-type 6 tonne payload vehicle, engineered for continuous day and or night shift operations for the drill and blast sector with an interchangeable payload.
​
This innovative platform features a unique self-levelling chassis on grade technology, a vision system with automated hole detection capabilities, and software integration to streamline operations.
​
The ARTEV™6000 can effectively navigate slopes of up to 15 degrees and 12-degree cross slopes while ensuring a stable chassis for payload deployment. Its dual and four-wheel driving functionality offers unparalleled flexibility for maneuvering when navigating the bench environment.
The ARTEV ™6000
​

SOLUTIONS PROVIDER
We build hi-tech, robust, wheeled vehicle solutions, specialising in the global mining industry.
Solutions that integrate the latest in technology improvements in Automation, AI, Robotics and Battery Technologies.
Mining managers are cognisant of the inherent physical, biological, ergonomic and environmental risks involved in mining today, thus prioritising the reduction of exposure hours to critical hazards is imperative for enhancing safety and risk mitigation in the workplace.
Manufactured in Western Australia our vehicles are equipped with a comprehensive array of sensors dedicated to the management of the mission, machine performance and the visibility for the operator from the comfort of the remote-control room.
Autonomy capabilities span from line-of-site to Level 4 autonomous control room operations, empowering operators to input QA activity with real time reporting. The Jevons solution demonstrates superior performance in executing repetitive tasks such as blast QA/QC, stemming and ANFO loading with precision, thereby enhancing productivity while concurrently lowering operating risks, carbon emissions and costs.
The vehicles payload agnostic feature facilitates seamless interchangeability of payloads on a single chassis, offering versatility beyond the conventional loading of bulk explosives and stemming material.
This mobility platform can be reconfigured based on customer needs to accommodate a range of alternative payloads including drilling fluids, de-watering equipment, sensors and monitoring equipment, geophysical sensors, even as a platform to manage the increasing number of electric cables in a pit as customers progress electrifying drills and shovels.​
THE ARTEV™6000 IS A GAME CHANGER
FIND OUT MORE
COMPLETING MISSIONS
Changing the future of mining means thinking differently.
All vehicles are custom built in-house and are capable of working on the toughest of terrain enabling our customers to access hazardous environments without putting their people in harms way.
Dynamic solutions, unmatched mobility, stability and versatility with the ability to complete missions on contoured, steep and unstable terrain.
Using groundbreaking perception-enabled sensor technology, the robot, a fully driverless vehicle is able to perform high precision positioning solutions.
​
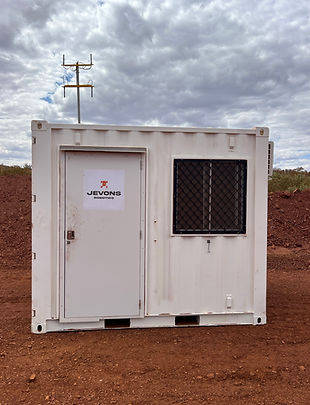.jpg)
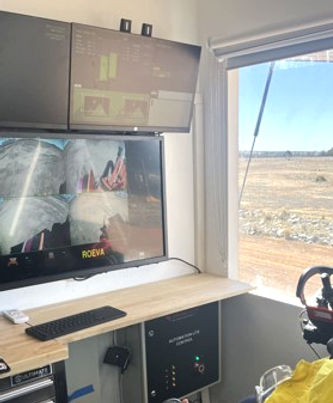
AIR CONDITIONED CENTRAL CONTROL ROOM. OPERATORS MAY BE RETRAINED TO BE CONTROL ROOM PILOTS
WHY JEVONS?
A new approach to create a safer workplace using revolutionary technology with greater benefits
REDUCES COSTS
> Replaces up to 7 operators with a single machine and pilot in contour blasting
> Access to multiple levels of autonomy outcomes from line of sight through to full automation
> Payload agnostic vehicles allowing for the integration of multiple payloads onto a single chassis
> Unique commercial model delivering lower cost of operations and improved returns on your capital
SAFETY FIRST
> Reduced exposure to risks of cavities
> Reduced exposure to manually handling explosives
> Reduced exposure to heat
> Reduced sprains and strains
> Reduced exposure to hazards of HV electric cables
​
INCREASES PRODUCTIVITY
> Day and night operations with real time data
> Drill hole consistency
> Sustained productivity of over 260 holes in a 12-hour shift
> Ability to digitise the workflows of manual process improving operational outcomes and compliance requirements
​
CLEAN
> Electric battery as a standard offer across the portfolio, zero tailpipe emissions replacing diesel light vehicles and stemming trucks

In the field
Safety first. Automated. Reduced costs. Increased productivity and Clean.


Current unsafe costly workplaces around the world.
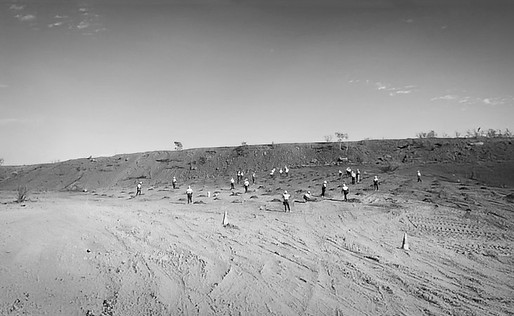